
.
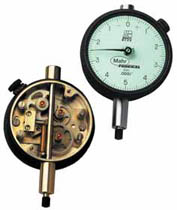
The American Society of Mechanical Engineers has the responsibility of preparing standards which encompass the inspection and the means of measuring various dimensional characteristics, as well as the instruments used to make those measurements. Since most dial indicators used in the United States are built to and used to measure inch specification, they generally do not fall under ISO specifications. Rather, ASME has updated old commercial and AGD standards into the most recent ASME B89.1.10-2000. This spec defines many aspects of dial indicators, including the various sizes, resolutions, and suggestions for construction, and of course, statements about performance.
Getting down to the nuts and bolts, a dial indicator is enclosed by a metal case that protects the instrument's mechanism. The case also serves as the rigid framework to support the means of amplifying the motion from the contact point to a hand moving against a graduated dial.
Why metal? With all the composites and plastics available one would think it would be easy to reduce costs by using a composite case. But we have to remember that we are in the measurement world here, and we can't go against certain basic measuring rules. In this case (no pun intended), the case is part of the measuring loop, and we know that temperature is one of the biggest contributors to measurement errors. If the case or any part of the indicator is not affected by temperature the same way as the part or the stand, then small errors will creep into the results.
They Point you in the Right Direction
Our mechanical indicators have precision gears and pinions for maximum accuracy. They are available in a wide variety of ranges, resolutions and
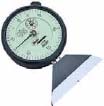
No comments:
Post a Comment